To Solve The Coating Anticorrosion Insufficient Small Expert - fumed Silica
Why does coating corrosion occur?
The coating itself: Some coatings contain corrosive substances, such as phenolic resin coatings containing free phenols, which will cause corrosion to the metal surface under certain conditions.
External factors, such as temperature, humidity, oxygen, pollutants, and other environmental factors, as well as improper metal surface treatment, may cause corrosion. For example, the metal surface is not thoroughly cleaned before painting, leaving impurities such as stains and grease, or the primer is not used as required, which may lead to corrosion.
Internal coating factors: There are pores and cracks inside the coating, and these defects may cause corrosion. The cracking, foaming, or peeling of the layer under the influence of environmental factors causes the coating to lose its protective effect on the substrate.
Coating adhesion problem: The adhesion between the coating and the substrate is insufficient, resulting in the coating easily peeling or peeling, thus losing its protective effect on the substrate.
Chemical media intrusion: water, acid, alkali, and other chemical media penetrate the coating through the pores and cracks of the coating, and chemical or electrochemical reactions occur with the metal surface, resulting in corrosion.
Coating aging: Affected by ultraviolet light, temperature, humidity, and other factors for a long time, the coating may appear aging phenomenon, such as cracking, powder, etc., thus losing its protective effect.
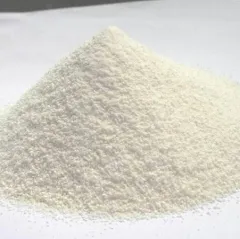
Properties of fumed silica:
Fumed silica is an amorphous silica with a nanoscale particle size, with an average particle size between 10-20 nanometers. Its unique structure and properties give it the following advantages in coatings:
Enhance the density of the coating: fumed silica nanoparticles can be filled in the pores and cracks in the coating, improving the density and coverage of the coating and reducing the possibility of penetration of corrosive media.
Improved coating adhesion: fumed silica nanoparticles can form a chemical bond with the organic polymer material in the coating, thereby improving the adhesion between the coating and the substrate and preventing the coating from peeling.
Enhanced wear and weather resistance of the coating: fumed silica nanoparticles can be evenly distributed in the coating, increasing the hardness and toughness of the coating and reducing scratches and wear while improving the weatherability and UV resistance of the coating.
The application of fumed silica in paint anticorrosion:
As a functional filler, fumed silica has a broad application prospect in coating anticorrosion. The following are the main application directions:
Anticorrosion coatings: fumed silica can be used as an additive to anticorrosion coatings to improve the anticorrosion properties of coatings. By introducing fumed silica into the coating, the compactness, adhesion, and wear resistance of the coating can be enhanced, thus effectively preventing the penetration and erosion of corrosive media.
Weather-resistant coating: fumed silica can improve the weather resistance of the coating so that it can maintain good performance when exposed to ultraviolet light, moisture, pollutants, and other environments for a long time. This helps to extend the life of the paint and maintain the aesthetics of the painted surface.
High-temperature coating: fumed silica has good thermal stability and can maintain good performance in high-temperature environments. Therefore, fumed silica can be applied to high-temperature coatings to improve the heat resistance and oxidation resistance of coatings to meet the need for corrosion protection in various extreme environments.
Heavy anticorrosive coatings: For occasions that need to withstand long-term corrosion of corrosive media, such as Marine environment, chemical equipment, etc., fumed silica can be used as an additive for heavy anticorrosive coatings.
The advantages of fumed silica in solving the insufficient anticorrosive coating:
Compared with traditional anticorrosive coatings, anticorrosive coatings with fumed silica have the following advantages:
Improved corrosion resistance: fumed silica can help extend the service life of the substrate and reduce the frequency of maintenance and replacement.
Reduced maintenance costs: By using fumed silica as an additive, you can reduce the amount of traditional anticorrosion coatings used. This is because fumed silica has high filling properties and can achieve good corrosion protection at lower concentrations. This helps to reduce painting costs and maintenance costs.
Strong adaptability: fumed silica has good chemical and thermal stability and can adapt to various environmental conditions and harsh application requirements. Whether indoor or outdoor, room temperature or high temperature, dry or humid environment, fumed silica can play an excellent anticorrosion effect.
Environmental protection and safety: fumed silica is a non-toxic and harmless nanomaterial, harmless to the environment and the human body. Compared with the toxic and harmful chemicals used in traditional anticorrosion coatings, the use of fumed silica is more environmentally friendly and safe.
Supplier of fumed silica:
Synthetic Chemical Nano Technology Co. Ltd., is an established global supplier of chemicals and manufacturers with more than 12 years experience. They offer super high quality chemical products, Nanomaterials, as well as graphite powder, boride powder, nanomaterials, and sulfide powder.
You can contact us to request high-quality Fused Silica Powder. (sales5@nanotrun.com)
Inquiry us