Research Progress and Application of Molybdenum Powder
Effect of Molybdenum Powder on Properties of Molybdenum Deep Processing Products:
Effect of particle size of molybdenum powder on properties of molybdenum deep processing products
The particle size of molybdenum powder is one of the critical factors affecting the properties of molybdenum deep processing products. Generally speaking, the finer molybdenum powder has a higher specific surface area and activity, which is conducive to improving the comprehensive performance of molybdenum deep processing products. Fine-grained molybdenum powder can have higher density and finer grain to improve the strength, toughness, corrosion resistance, and other properties of molybdenum deep processing products. Therefore, molybdenum deep processing products should be selected as raw material when preparing molybdenum powder with finer particle size.
The influence of the purity of molybdenum powder on the performance of molybdenum deep processing products
High-purity molybdenum powder can obtain higher-purity deep-processing products, improving its performance. In addition, the high-purity molybdenum powder can also reduce the introduction of impurities in the preparation process and improve the purity and quality of the product.
The impact of impurity content of molybdenum powder on the performance of molybdenum deep processing products
Impurity elements such as iron, silicon, calcium, and so on seriously affect the performance of molybdenum deep-processing products. For example, iron will reduce the corrosion resistance of molybdenum deep-processed products, silicon will reduce the product's toughness, and calcium will promote the growth of grains, affecting the strength and toughness of the product. Therefore, when preparing molybdenum deep-processed products, molybdenum powder with lower impurity content should be selected as raw material.
The impact of other factors on the performance of molybdenum deep processing products
In addition to the above factors, other factors also affect the performance of molybdenum deep-processing products. For example, the preparation process, heat treatment system and other factors will also affect the organization and performance of the product. These factors require strict control and management during the preparation process to ensure the quality and performance of the product.
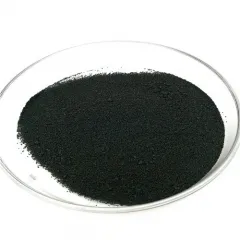
Applications of Molybdenum Powder:
Iron and steel industry
Molybdenum powder is mainly used in the steel industry to produce special steel. Molybdenum powder has high strength, toughness, corrosion resistance and other characteristics, so it is widely used to manufacture high-strength structural steel, wear-resistant steel, corrosion-resistant steel and other special steels. Adding molybdenum powder can improve the strength, toughness, corrosion resistance, and other steel properties so that it has a longer service life and higher reliability.
The electronics industry
Molybdenum powder is mainly used in the electronics industry to manufacture electronic components and circuit boards. Adding molybdenum powder can improve the electrical conductivity and stability of electronic components and circuit boards, and the quality and reliability of electronic products can be improved.
Medical device field
In the field of medical devices, molybdenum powder is mainly used in the manufacture of medical device parts and biomedical materials. Molybdenum powder is widely used to manufacture medical device components and biomedical materials. For example, molybdenum powder can make parts for medical devices such as artificial joints and dental implants, as well as biomedical materials such as bioceramics.
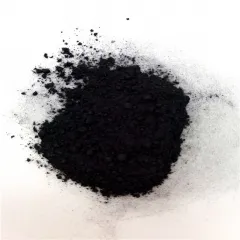
Preparation Technology and Progress of Molybdenum Powder:
Traditional preparation method
The traditional preparation methods of molybdenum powder mainly include reduction and oxidation methods. The reduction method is one of the most commonly used methods, which reduces molybdenum oxide to molybdenum powder by using reducing agents (such as hydrogen, ammonia, etc.) at high temperatures. The oxidation rule is oxidizing metal molybdenum to molybdenum dioxide and then reducing it to molybdenum powder. Although these methods can obtain a certain quality of molybdenum powder, there are high production costs, low output, coarse particles and other problems, so it isn't easy to meet the needs of modern industry.
Advanced preparation methods
Researchers continue to explore new preparation techniques and methods to solve the shortcomings of traditional preparation methods. In recent years, some advanced preparation methods have been gradually applied, including vapour deposition, liquid deposition, mechanical alloying, etc.
Vapour deposition method
Vapour deposition is preparing powder by reacting in a gaseous or vapour state. In vapour deposition, the raw material can be converted into a compound in a gaseous or vapour state through a chemical or physical reaction, then deposited into a powder during cooling or crystallization. Molybdenum powder with high purity and fine particles can be obtained by vapour deposition. Still, it has not been widely used because of the problems of high reaction temperature and low yield.
Liquid deposition method
Liquid deposition is preparing powder by reacting in a liquid state. Then, the raw material in the solution can be converted into a powder by means of a chemical reaction or physical change. Molybdenum powder with high purity and fine particles can be obtained by liquid deposition, but it has not been widely used because of complex reaction conditions and low yield.
Mechanical alloying method
Mechanical alloying prepares alloy powder by grinding metal powder in a high-energy ball mill. In the mechanical alloying method, the metal powder can be put into the ball mill with the right amount of additives for a specific time to obtain the alloy powder. The mechanical alloying method can obtain high purity, fine particles of molybdenum powder, but because the ball milling process will produce a lot of heat, resulting in powder sintering or oxidation and other problems, the need to take corresponding measures to control the quality of the powder.
Progress and trend
With the continuous development of science and technology, molybdenum powder preparation technology and methods are also constantly improving. At the same time, with the continuous emergence of new materials and application fields, the application prospects of molybdenum powder will also be broader. In the future, new preparation technologies and methods must be further studied to obtain higher performance and higher quality molybdenum powder to meet the needs of different fields.
Inquiry us